Got started on the wiring process for this thing!
Last 6/8 months I’ve been researching wiring pretty heavily, bought a couple HPA courses that were super helpful and joined a couple Facebook groups with a lot of great info.
Originally the plan was to strip all the smog and AC stuff off the engine bay harness, and the interior harness and then clean it up. After we tore the stock harness out of the truck, I jumped into the interior harness first and honestly just fucked it all up haha. I deloomed it and didn’t zip tie the wires as I was thinning the unneeded wires out so when it was all thinned out, the rats nest of wires that was there was a huge mess. I learned my lesson after that and zip tied all the wire harnesses and the pulled wires out one by one, tightening the zip tie to keep its uniform shape.
Pretty much the only stock wiring I’m using at this point is the engine harness, and the bare
minimum of wires needed to go to the PCM. Everything else I’m redoing, because why put 30 year old wiring on this thing haha.
Started with making a mock up rope harness for the rear of the truck. Everything on the rear of the truck will go through an HDP20 29 pin plug. The main harness branch will have DT connectors for things like removal of the bedsides/tail lights, removing the fuel pump, a roof LED rack. Everything is being ran down the passenger side of the truck and will be wrapped with the appropriate sheathing to protect from the exhaust etc while fuel related will be kept to the drivers side of the truck.
3/8 size rope is used due to it being similar to how a wire lays down and doesn’t kink when you bend it. Smaller diameter rope will allow some kinks and bends you should try to avoid. Zip ties and painters tape is your friend with anything wiring I have learned.
Anyways enough yappin, 6ish hours and a couple hazys and we had a complete mock up rear harness! Got it laid out on some peg board and am excited to knock this out.
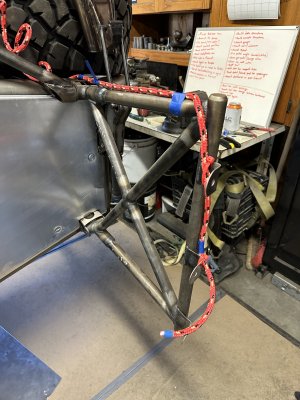
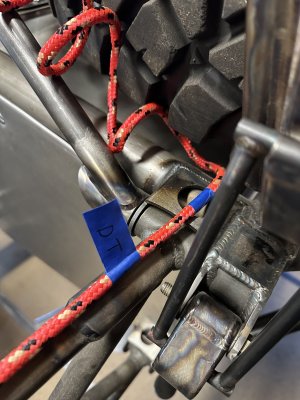
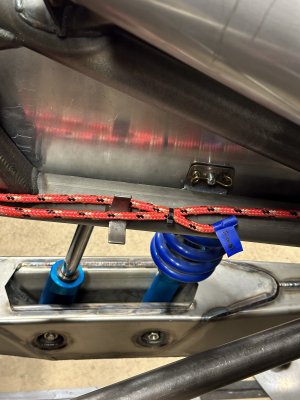
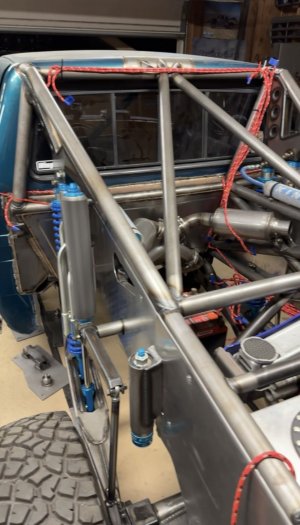
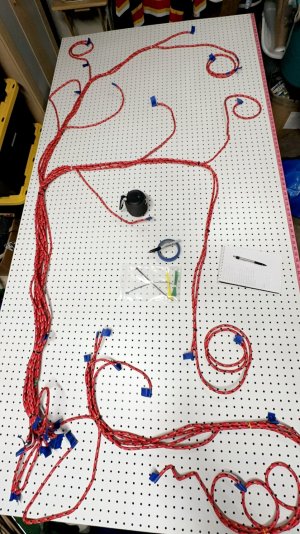
Edit: I don’t think I said harness enough
