Camper shell fun
Well-known member
- Joined
- Jun 10, 2022
- Messages
- 94
Hey dudes I’m not sure who on here knows that I work at TC and have for the last almost 18 years, but I have been working on this project for the last just over two years. I put my blood sweat and tears into this project end it’s pretty satisfying to finally be able to talk about it. I originally just designed these for my own truck because after I had my son I realized I did not want to have a lower ball joint failure with him in the car so I got to work. I now know more about these front ends than I ever wanted to but at least it’s done. Anyhow, yes I know they are expensive but trust me they were not cheap to make. I have 30,000 miles on mine and my coworker has another 5k on his. As some of you may know I’m not exactly easy on my truck so you can guarantee that they have been tested for durability. Check them out and please help me spread the word so that people stop busting lower ball joints and totaling their trucks. Sorry for any typos this is talk texting.
https://www.chaosfab.com/product/1996-2004-Toyota-Tacoma-Lower-Uniball-Conversion-OE-Tie-Rod
https://www.chaosfab.com/product/1996-2004-Toyota-Tacoma-Lower-Uniball-Conversion-Heim-Steering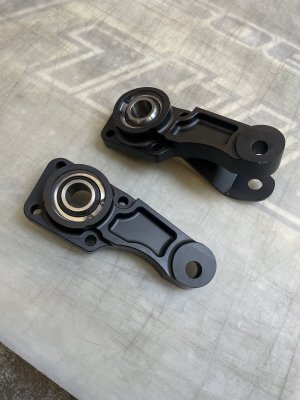
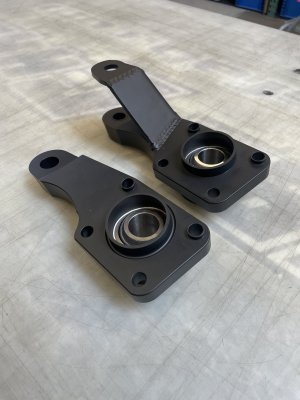
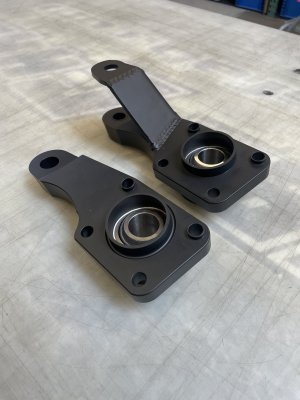
This last picture is the first prototype that I did a year and a half ago that was made by hand
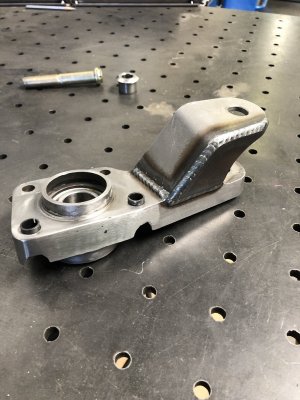
https://www.chaosfab.com/product/1996-2004-Toyota-Tacoma-Lower-Uniball-Conversion-OE-Tie-Rod
https://www.chaosfab.com/product/1996-2004-Toyota-Tacoma-Lower-Uniball-Conversion-Heim-Steering
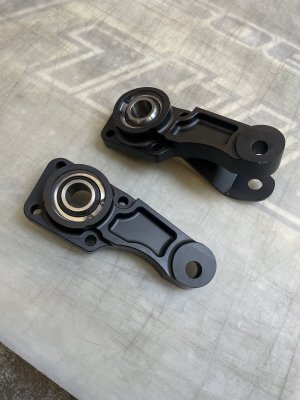
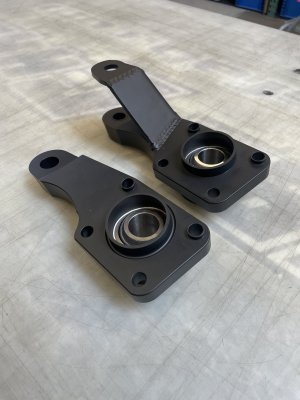
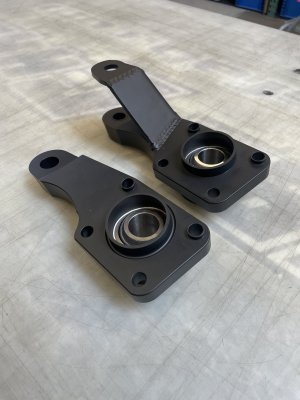
This last picture is the first prototype that I did a year and a half ago that was made by hand
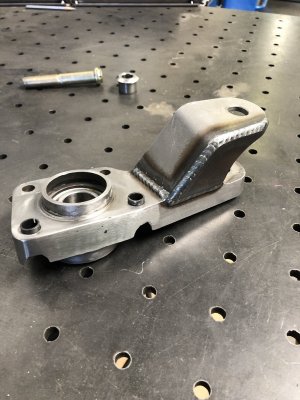