Ok got rear 3rd all regeared with 4.86 gears. Rpm is much better for all around driving with the 35s. 0 noise. Just drained the 85w-140 so ill use that in the front diff. No metal or anything in the rear gear oil and all was good looking through fill plug.
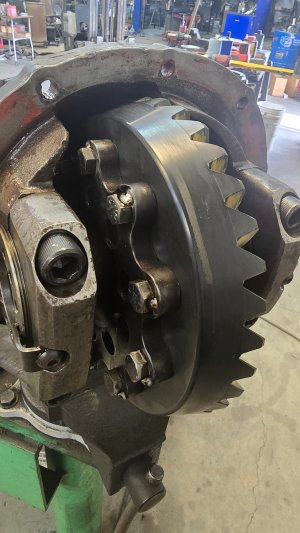
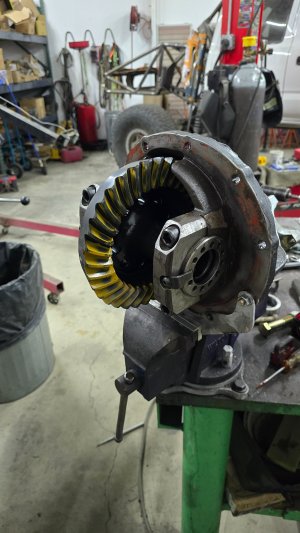
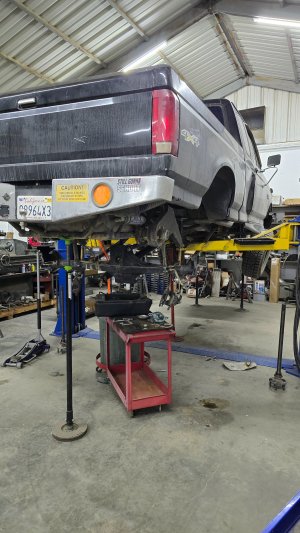
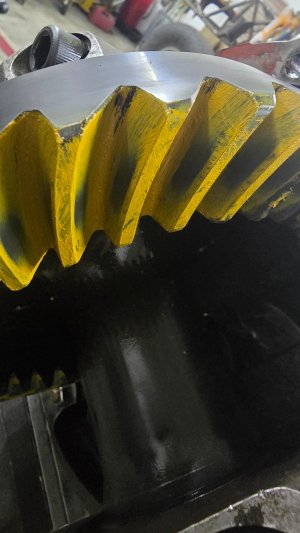
Had a king snake come inspect my work in the shop, he was happy with the work so I carried him back outside in the bushes.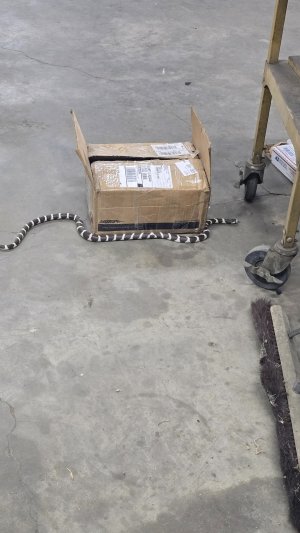
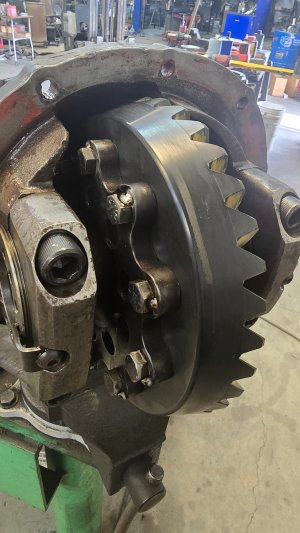
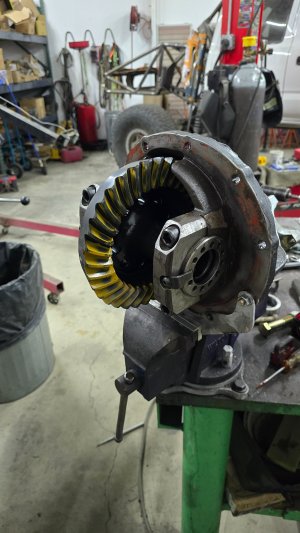
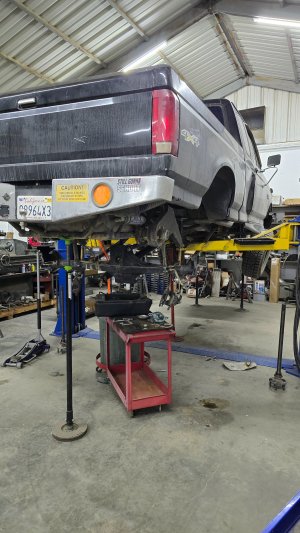
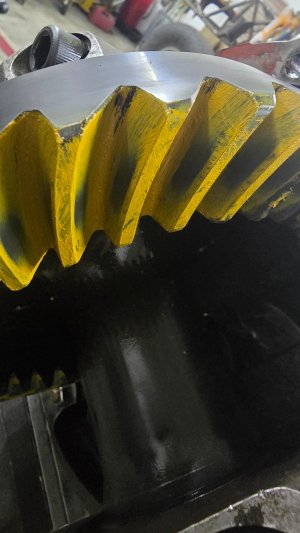
Had a king snake come inspect my work in the shop, he was happy with the work so I carried him back outside in the bushes.
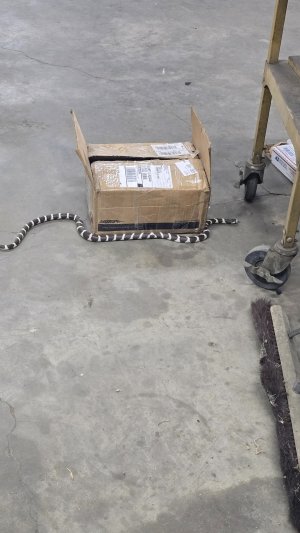