UR_Mawm69
Well-known member
Ok, this thread is just going to be for notching help / pics / ideas / just everything. Steve-to the-E / Wall-to the-E said he'll move the thread after they make an appropriate sub-thread for fabrication stuff.
Honestly, I WISH I would of made this thread or someone else did back when I was constantly building shit and fabricating (not doing gay yoga shit, like now).
I always look at build threads, like Tommy's I was just looking at, and see all your copes/joints and think HOW THE FUCK DO YOU GET THEM SO CLEAN AND PERFECT for the weld your going to do?!?!?!? If i made notches that perfect, my welds would look tittyrific as well!!!!!!!
Now....... I say unfortunately now, but back when my cousin had initially taught me how to cut/notch tubing/build things, it made everything go by MUCH FASTER and I wasn't trying to make titty perfect welds and whatnot. He showed my how to notch a tube for a 90* perpendicular joint, with the chop saw. Just take the one side of the clamp on the saw, completely off so that I can hold the tube at any angle. Just hold on tight, and press the saw down SLOW. Because then it left a little flared bevel to fill with the weld. It didn't leave the gap missing/a flat/flush joint to weld onto, which ending up with a raised/booger weld, so to say.
(idk if this is making fucking sense but idk how to explain it, or anything for that matter anymore. hah)
He showed my to hold it in the chop saw a little angled this way/that way for a deeper notch hear on this side and not so deep on the opposite side. Then i can do a 45* joint with the tubes. Just clean it up with a flap wheel after, to make it fit flushER.
So that's how I've notched 99* of every fucking tube i've used to build something in the past 15 years. I'm pretty sure i've used a notcher here and there or tried this one, tried that one, I've even used the $50k one that SDHQ had in their shop one of the like 4 or 5 times I've worked(hah) there before. Which did end up with a perfect notch, just burnt the fuck out of that end of the tube. blah blah blah.
soooooooooooooo.................. how is everyone notching their tubes / what are you using / what stories do you have about ALMOST cutting your fingys off maybe (like me in the chop saw)
Pics are from Tommy's 4x4 ttb 69 f100, or whatever, thread just because there's a lot of reading. so im rewarding you fucks with some cool pics. haha..........
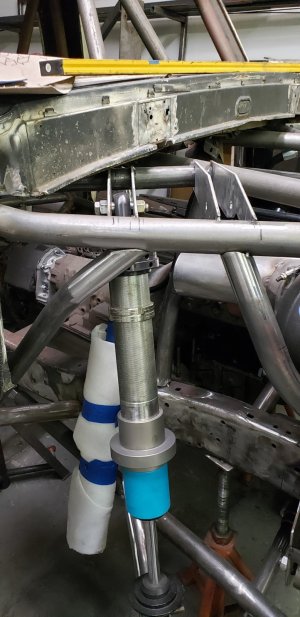
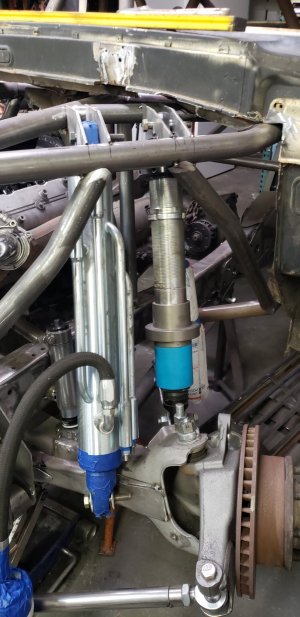
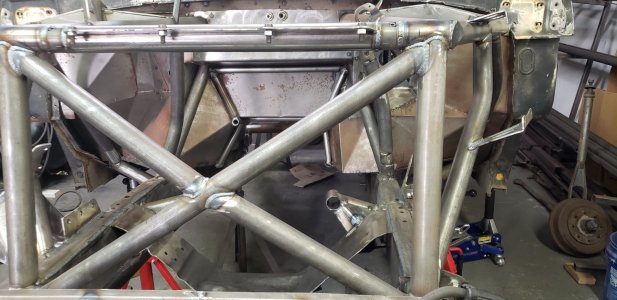
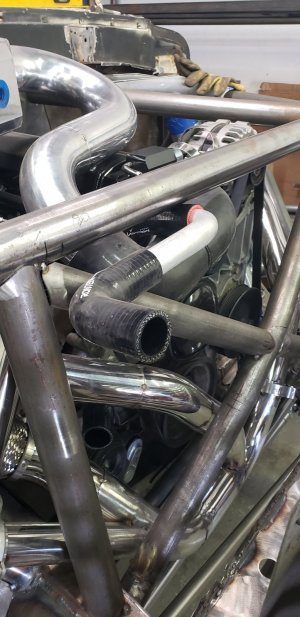
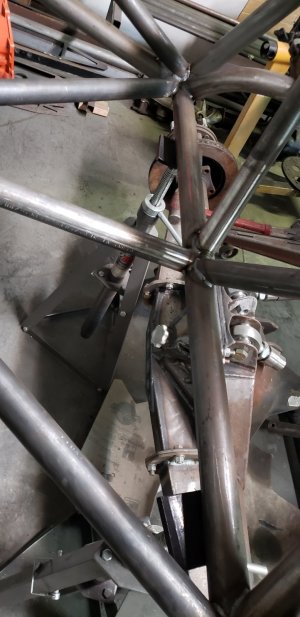
Honestly, I WISH I would of made this thread or someone else did back when I was constantly building shit and fabricating (not doing gay yoga shit, like now).
I always look at build threads, like Tommy's I was just looking at, and see all your copes/joints and think HOW THE FUCK DO YOU GET THEM SO CLEAN AND PERFECT for the weld your going to do?!?!?!? If i made notches that perfect, my welds would look tittyrific as well!!!!!!!
Now....... I say unfortunately now, but back when my cousin had initially taught me how to cut/notch tubing/build things, it made everything go by MUCH FASTER and I wasn't trying to make titty perfect welds and whatnot. He showed my how to notch a tube for a 90* perpendicular joint, with the chop saw. Just take the one side of the clamp on the saw, completely off so that I can hold the tube at any angle. Just hold on tight, and press the saw down SLOW. Because then it left a little flared bevel to fill with the weld. It didn't leave the gap missing/a flat/flush joint to weld onto, which ending up with a raised/booger weld, so to say.
(idk if this is making fucking sense but idk how to explain it, or anything for that matter anymore. hah)
He showed my to hold it in the chop saw a little angled this way/that way for a deeper notch hear on this side and not so deep on the opposite side. Then i can do a 45* joint with the tubes. Just clean it up with a flap wheel after, to make it fit flushER.
So that's how I've notched 99* of every fucking tube i've used to build something in the past 15 years. I'm pretty sure i've used a notcher here and there or tried this one, tried that one, I've even used the $50k one that SDHQ had in their shop one of the like 4 or 5 times I've worked(hah) there before. Which did end up with a perfect notch, just burnt the fuck out of that end of the tube. blah blah blah.
soooooooooooooo.................. how is everyone notching their tubes / what are you using / what stories do you have about ALMOST cutting your fingys off maybe (like me in the chop saw)
Pics are from Tommy's 4x4 ttb 69 f100, or whatever, thread just because there's a lot of reading. so im rewarding you fucks with some cool pics. haha..........
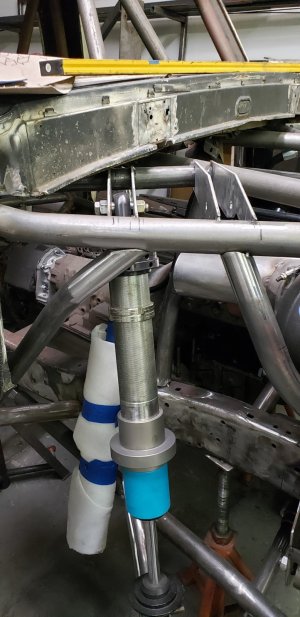
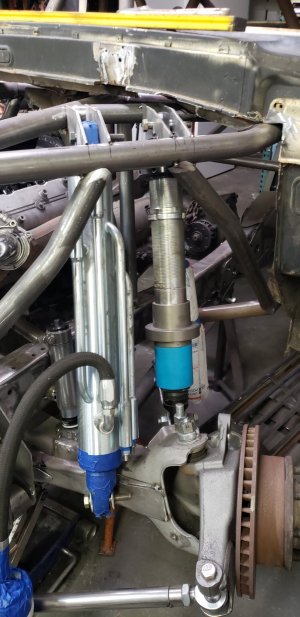
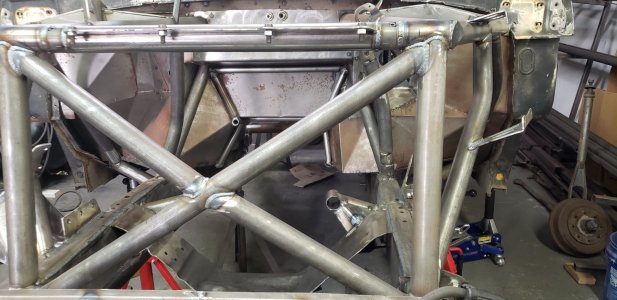
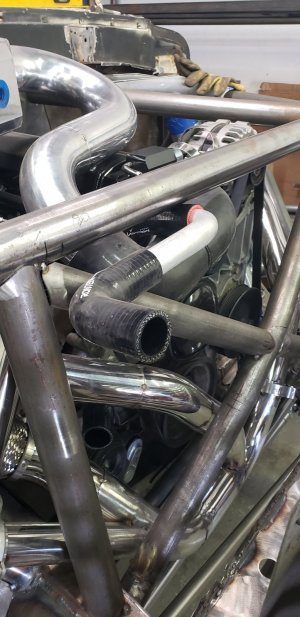
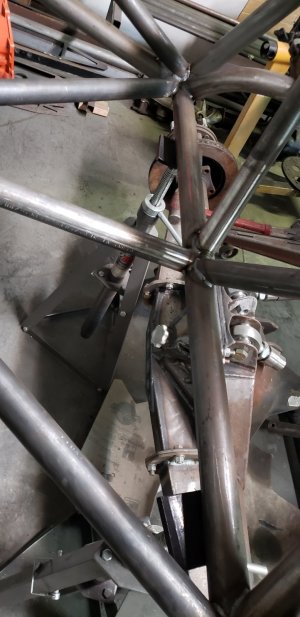